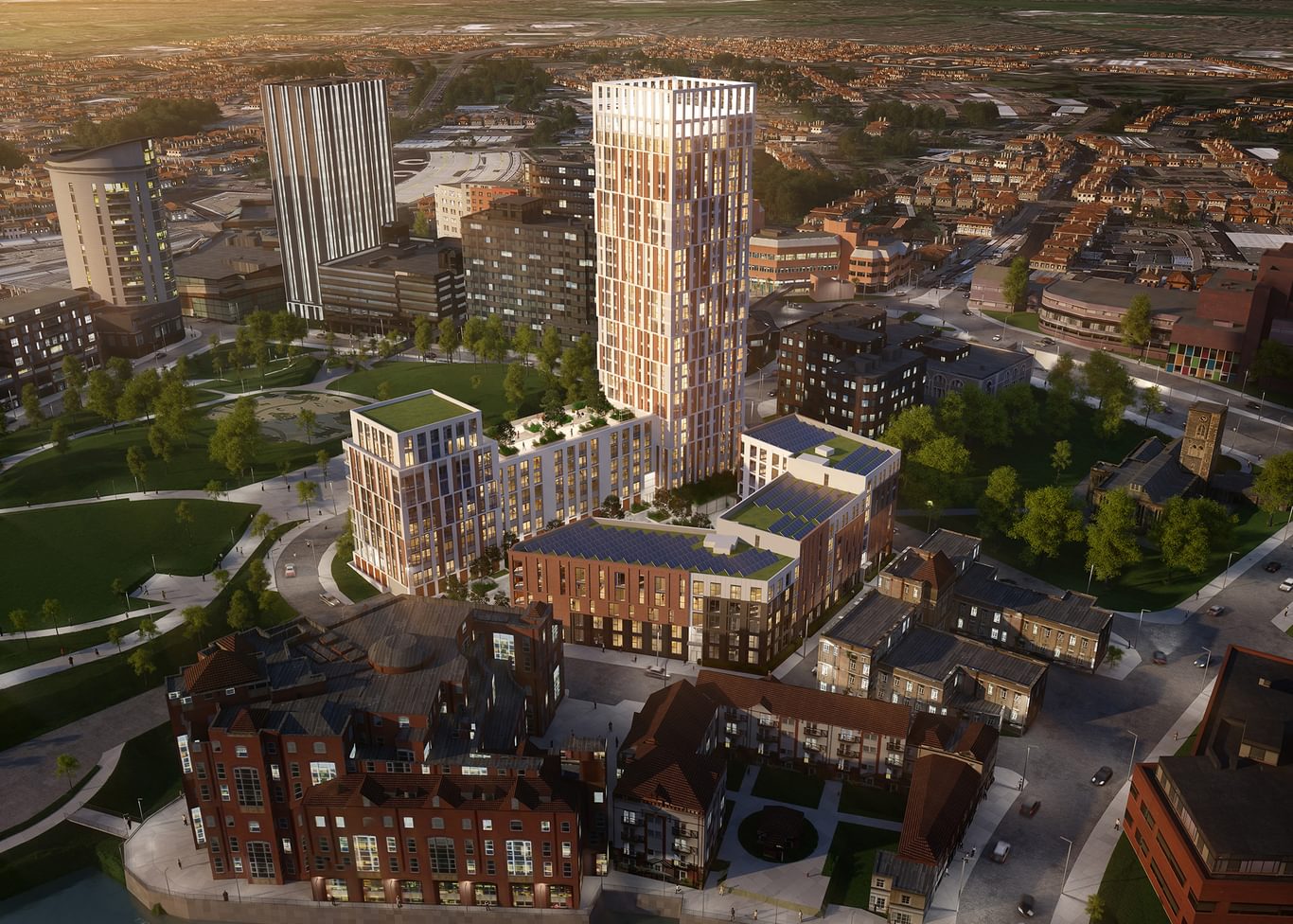
Designing for world-class façade safety at Bristol’s Castle Park View
Industrialización: Fachadas prefabricadas con estándares de seguridad de clase mundial en el Residencial Castle Park View en Bristol, UK
Chapman Taylor has been working with Bouygues UK and leading industry experts to develop a bespoke façade system which combines the highest standards of fire safety with strong aesthetic appeal for our Castle Park View residential development in central Bristol.
The groundbreaking project, designed by Chapman Taylor for LinkCity, is currently under construction on site, where we are working with Bouygues UK on the delivery phase (as well as on the interior design).
The façade design process for Castle Park View has involved detailed discussions with leading authorities on fire safety, rigorous material testing and data analysis, adding to our in-depth knowledge of the very latest façade safety standards. The Castle Park View façade now meets fire safety standards to a degree matched by only a few other developments of this type in the UK.
Industry-leading façade standards
Castle Park View will regenerate a brownfield site in a prime location on the south-eastern corner of Castle Park. A 26-storey tower, the tallest structure in Bristol, and a 10-storey block will book-end the main building, which fronts onto a park. The strong built form along the northern boundary will be reminiscent of the old castle wall which once stood on the site. The landmark building will provide 375 high-quality homes through a mixture of Build-to-Rent and affordable housing. Car/bicycle spaces and leisure facilities are also provided, along with a 24/7 concierge reception.
It was important to us that the cladding was tailored to fit its surroundings and to reflect the site’s history as well as the wider urban grain. We initially explored the use of an “off-the-shelf” cladding system for the building, which would have circumvented the need for us to implement rigorous testing on every component of the façade. However, led by our desire to create a strong visual presence in the city and the contractor’s need for a safe, quick and easy-to-install envelope, we were able to progress our design of a bespoke cladding system.
This cladding system required bespoke testing in a purpose-made laboratory in Luxembourg, where we were able to test fire safety, impact resistance, weather performance and pressure resistance on every element of the façade to ensure that everything conformed to the very highest safety standards.
All the materials used across the entire façade (Moca Creme stone, inset clay bricks, window panels and spandrel panels) are fire-resistant, each at the highest Euroclass A1 standard for fire performance (the underlying membranes and EPDM materials are Euroclass B standard, which is the highest currently available on the market and only used in limited areas). This means that Castle Park View will have one of the highest performing fire-safe façades for buildings of this type in the whole UK.
Testing and selection
The original design for the façade included fritted, back-painted, laminated glass spandrel panels between floors and as corner features, which provided an attractive visual cover for the concrete columns and other structural elements within the building. This glass was successfully impact-tested to meet CWCT (Centre for Window and Cladding Technology) requirements by an approved testing facility.
However, revised Building Regulations introduced after the Grenfell Tower tragedy relating to fire safety require that laminated glass can only be used in clear-vision glazing within window frames due to the limited combustibility of this material. We regularly met senior fire safety experts at the NHBC (National House Building Council), which is the industry leader in the building insurance sector, to examine the proposals in detail. These discussions gave us a more detailed understanding of the very latest and highest building façade fire safety requirements.
While there is a technical argument to be had regarding the use of this material in façades, it became clear that this would not be an acceptable solution, so we worked with the NHBC to change the design. We sought to examine several possible alternatives to avoid the need for a revised planning application, or else to ensure that we were on a sound footing in submitting such an application.
Heat-strengthened, back-painted glass was suggested to us as an alternative, so we arranged rigorous impact tests on various thicknesses and frits. However, the results made clear that this type of glass was not able to withstand strong force and we rejected it as unsuitable for a tall building such as Castle Park View. One reason for the failure is that the process by which back-painted glass is created weakens the integrity of the glass.
Instead, we devised a solution which creates a pleasing aesthetic effect while optimising building safety – using opaque, powder-coated aluminium sheets, colour-matched to the window frames, instead of glass. The powder coating is a subtle and attractive grey, which poses no problems from a fire safety point of view (certain other colours, such as red and orange, can be problematic). This formed the basis for a successful revised planning application.
The many benefits of off-site façade manufacture
The high quality of the solution, and of the overall façade, has been enhanced by the fact that the façade has been created off-site as a unitised modular system. Cladding panels, each containing stone, brick, windows and spandrels, have been assembled off-site in factories in Poland and Portugal – then delivered to the site ready to be fixed to the building exterior.
Off-site construction can make a great difference to the detailing and quality of the built product because of the ability to control the conditions in which work is carried out. The panels achieve a high degree of airtightness and weathertightness as well as thermal and acoustic efficiency, with the entire façade designed to slot into place as a unified system.
It also allows for greater programme efficiency because off-site construction can continue when bad weather or other circumstances would otherwise have slowed or suspended construction on site. The recent COVID-19 pandemic required many sites to shut or to slow construction considerably to ensure safe distancing between workers, but off-site construction does not require large site teams working in close proximity. Site safety is also improved by removing the need to carry materials out onto the envelope at the higher levels.
Experts in safety-conscious design
It is a fundamental design principle for Chapman Taylor that the health and safety of contractors, residents, maintenance staff, visitors and neighbours is paramount when designing tall buildings, including their façades. Ensuring compliance with current regulations is imperative, as well as considering global best practice to ensure buildings are safe and easily adaptable to meet future requirements and stand the test of time. Our experience in designing and delivering Castle Park View in Bristol is one example among many of our industry-leading knowledge of, and expertise in, how to design tall buildings, whether residential, office or mixed-use, to the highest safety standards while providing attractive, memorable and context-appropriate landmarks on the urban skyline.
Chapman Taylor ha estado trabajando con Bouygues UK y los principales expertos de la industria para desarrollar un sistema de fachada a medida que combine los más altos estándares de seguridad contra incendios con un fuerte atractivo estético para nuestro desarrollo residencial Castle Park View en el centro de Bristol.
El innovador proyecto, diseñado por Chapman Taylor para LinkCity y M&G, se encuentra actualmente en construcción y avanza correctamente. Chapman Taylor se coordina con Bouygues UK para la etapa de entrega del proyecto y también está proporcionando servicios de interiorismo en los apartamentos y servicios comunes.
El proceso de diseño de fachadas para Castle Park View ha involucrado también a las principales autoridades sobre seguridad contra incendios, pruebas rigurosas de materiales, análisis de datos, todo ello unido a nuesta experiencia en el conocimiento de los últimos estándares de seguridad de fachadas.
Industry-leading façade standards
Castle Park View will regenerate a brownfield site in a prime location on the south-eastern corner of Castle Park. A 26-storey tower, the tallest structure in Bristol, and a 10-storey block will book-end the main building, which fronts onto a park. The strong built form along the northern boundary will be reminiscent of the old castle wall which once stood on the site. The landmark building will provide 375 high-quality homes through a mixture of Build-to-Rent and affordable housing. Car/bicycle spaces and leisure facilities are also provided, along with a 24/7 concierge reception.
It was important to us that the cladding was tailored to fit its surroundings and to reflect the site’s history as well as the wider urban grain. We initially explored the use of an “off-the-shelf” cladding system for the building, which would have circumvented the need for us to implement rigorous testing on every component of the façade. However, led by our desire to create a strong visual presence in the city and the contractor’s need for a safe, quick and easy-to-install envelope, we were able to progress our design of a bespoke cladding system.
This cladding system required bespoke testing in a purpose-made laboratory in Luxembourg, where we were able to test fire safety, impact resistance, weather performance and pressure resistance on every element of the façade to ensure that everything conformed to the very highest safety standards.
All the materials used across the entire façade (Moca Creme stone, inset clay bricks, window panels and spandrel panels) are fire-resistant, each at the highest Euroclass A1 standard for fire performance (the underlying membranes and EPDM materials are Euroclass B standard, which is the highest currently available on the market and only used in limited areas). This means that Castle Park View will have one of the highest performing fire-safe façades for buildings of this type in the whole UK.
Testing and selection
The original design for the façade included fritted, back-painted, laminated glass spandrel panels between floors and as corner features, which provided an attractive visual cover for the concrete columns and other structural elements within the building. This glass was successfully impact-tested to meet CWCT (Centre for Window and Cladding Technology) requirements by an approved testing facility.
However, revised Building Regulations introduced after the Grenfell Tower tragedy relating to fire safety require that laminated glass can only be used in clear-vision glazing within window frames due to the limited combustibility of this material. We regularly met senior fire safety experts at the NHBC (National House Building Council), which is the industry leader in the building insurance sector, to examine the proposals in detail. These discussions gave us a more detailed understanding of the very latest and highest building façade fire safety requirements.
While there is a technical argument to be had regarding the use of this material in façades, it became clear that this would not be an acceptable solution, so we worked with the NHBC to change the design. We sought to examine several possible alternatives to avoid the need for a revised planning application, or else to ensure that we were on a sound footing in submitting such an application.
Heat-strengthened, back-painted glass was suggested to us as an alternative, so we arranged rigorous impact tests on various thicknesses and frits. However, the results made clear that this type of glass was not able to withstand strong force and we rejected it as unsuitable for a tall building such as Castle Park View. One reason for the failure is that the process by which back-painted glass is created weakens the integrity of the glass.
Instead, we devised a solution which creates a pleasing aesthetic effect while optimising building safety – using opaque, powder-coated aluminium sheets, colour-matched to the window frames, instead of glass. The powder coating is a subtle and attractive grey, which poses no problems from a fire safety point of view (certain other colours, such as red and orange, can be problematic). This formed the basis for a successful revised planning application.
The many benefits of off-site façade manufacture
The high quality of the solution, and of the overall façade, has been enhanced by the fact that the façade has been created off-site as a unitised modular system. Cladding panels, each containing stone, brick, windows and spandrels, have been assembled off-site in factories in Poland and Portugal – then delivered to the site ready to be fixed to the building exterior.
Off-site construction can make a great difference to the detailing and quality of the built product because of the ability to control the conditions in which work is carried out. The panels achieve a high degree of airtightness and weathertightness as well as thermal and acoustic efficiency, with the entire façade designed to slot into place as a unified system.
It also allows for greater programme efficiency because off-site construction can continue when bad weather or other circumstances would otherwise have slowed or suspended construction on site. The recent COVID-19 pandemic required many sites to shut or to slow construction considerably to ensure safe distancing between workers, but off-site construction does not require large site teams working in close proximity. Site safety is also improved by removing the need to carry materials out onto the envelope at the higher levels.
Experts in safety-conscious design
It is a fundamental design principle for Chapman Taylor that the health and safety of contractors, residents, maintenance staff, visitors and neighbours is paramount when designing tall buildings, including their façades. Ensuring compliance with current regulations is imperative, as well as considering global best practice to ensure buildings are safe and easily adaptable to meet future requirements and stand the test of time. Our experience in designing and delivering Castle Park View in Bristol is one example among many of our industry-leading knowledge of, and expertise in, how to design tall buildings, whether residential, office or mixed-use, to the highest safety standards while providing attractive, memorable and context-appropriate landmarks on the urban skyline.
Fachadas Industrializadas - Estándares Superiores
Castle Park View es un proyecto de regeneración urbana. Un edificio de 26 plantas que será el más alto de Bristol y un bloque de 10 plantas que será el edificio principal y que da al parque. Formas rotundas a lo largo del límite norte del terreno serán la reminiscencia de la antigua muralla del castillo ya desaparecida. Éste edificio emblemático dota de 375 viviendas de alta calidad en régimen de alquiler “build to rent” y fácil accesibilidad y asequibles a gran parte de la población local que incluyen espacios para bicis/coches, espacios de entretenimiento variado y servicios de conserjería las 24 horas, todos los días.
Para nosotros de vital importancia que el diseño de la fachada se adaptara a su entorno y reflejara la historia del lugar y su respeto al entorno urbano natural de esa parte de la ciudad. Inicialmente exploramos el uso de un sistema de revestimiento " off-the-shelf " lo que habría evitado la necesidad de realizar pruebas rigurosas en cada componente de la fachada. Sin embargo, motivados por nuestro deseo de crear una fuerte presencia visual en la ciudad y la necesidad del contratista de un crear una piel segura, rápida y fácil de instalar, pudimos avanzar en el diseño de un sistema de revestimiento, de calidad e industrializado, a medida.
Este sistema de revestimiento requirió pruebas en un laboratorio donde se probaron la resistencia al impacto, el efecto del clima y la resistencia a la presión en cada elemento de la fachada para garantizar que el sistema cumpliera con las Regulaciones de Construcción del Reino Unido y los estándares británicos apropiados.
Todos los materiales utilizados en la fachada (piedra Moca Creme, ladrillos de arcilla empotrados, paneles para carpintería y paneles spandrel) son altamente resistentes al fuego con el estándar más alto de Euroclass A1 para el rendimiento contra incendios (las membranas subyacentes y los materiales EPDM son el estándar Euroclass B, que es el más alto actualmente disponible en el mercado y solo se usa en áreas limitadas).
Testing and selection
The original design for the façade included fritted, back-painted, laminated glass spandrel panels between floors and as corner features, which provided an attractive visual cover for the concrete columns and other structural elements within the building. This glass was successfully impact-tested to meet CWCT (Centre for Window and Cladding Technology) requirements by an approved testing facility.
However, revised Building Regulations introduced after the Grenfell Tower tragedy relating to fire safety require that laminated glass can only be used in clear-vision glazing within window frames due to the limited combustibility of this material. We regularly met senior fire safety experts at the NHBC (National House Building Council), which is the industry leader in the building insurance sector, to examine the proposals in detail. These discussions gave us a more detailed understanding of the very latest and highest building façade fire safety requirements.
While there is a technical argument to be had regarding the use of this material in façades, it became clear that this would not be an acceptable solution, so we worked with the NHBC to change the design. We sought to examine several possible alternatives to avoid the need for a revised planning application, or else to ensure that we were on a sound footing in submitting such an application.
Heat-strengthened, back-painted glass was suggested to us as an alternative, so we arranged rigorous impact tests on various thicknesses and frits. However, the results made clear that this type of glass was not able to withstand strong force and we rejected it as unsuitable for a tall building such as Castle Park View. One reason for the failure is that the process by which back-painted glass is created weakens the integrity of the glass.
Instead, we devised a solution which creates a pleasing aesthetic effect while optimising building safety – using opaque, powder-coated aluminium sheets, colour-matched to the window frames, instead of glass. The powder coating is a subtle and attractive grey, which poses no problems from a fire safety point of view (certain other colours, such as red and orange, can be problematic). This formed the basis for a successful revised planning application.
Prueba y selección
El diseño original de la fachada incluye paneles de vidrio laminado templado, pintados a contraluz que proporcionan una atractiva cubierta visual para las columnas de hormigón y otros elementos estructurales dentro del edificio. Este vidrio fue probado con éxito para cumplir con los requisitos de CWCT (Centro de Tecnología de Ventanas y Revestimientos) en distintas pruebas de instalación previa.
Sin embargo, las Regulaciones de Construcción revisadas introducidas después de la tragedia de la Torre Grenfell relacionadas con la seguridad contra incendios requieren que el vidrio laminado solo se pueda usar en acristalamientos de visión clara dentro de marcos de ventanas debido a la limitada combustibilidad de este material. El equipo se reunió regularmente con expertos superiores en seguridad contra incendios en el NHBC (National House Building Council), líder de la industria en el sector de seguros de construcción, para examinar las propuestas en detalle. Estas discusiones nos ayudaron a obtener una comprensión detallada de los últimos y más altos requisitos de seguridad contra incendios en fachadas de edificios.
Si bien existe una base técnica que podría utilizarse para respaldar el uso de este material como parte de las fachadas, quedó claro que esta no sería una solución aceptable según las regulaciones actuales, por lo que el equipo trabajó con el NHBC para cambiar y actualizar el diseño. Intentamos examinar varias alternativas posibles para evitar la necesidad de una solicitud de planificación revisada o de lo contrario para asegurarnos de que estamos en condiciones de presentar una solicitud de este tipo.
Como alternativa, se sugirió vidrio con pintura posterior reforzada con calor, por lo que el equipo organizó rigurosas pruebas de impacto en varios espesores y temperaturas. Sin embargo, los resultados dejaron en claro que este tipo de vidrio no fue capaz de resistir fuerzas excesivas y fue rechazado como inadecuado para un edificio alto como Castle Park View.
Finalmente conseguimos diseñar una solución que crea un efecto estético agradable al tiempo que optimiza la seguridad del edificio mediante el uso de láminas de aluminio opacas, con recubrimiento de polvo, que coinciden con el color de los marcos de las ventanas, en lugar de vidrio. El recubrimiento en polvo es un gris sutil y atractivo que no plantea problemas desde el punto de vista de seguridad contra incendios (ciertos otros colores, como el rojo y el naranja, pueden ser problemáticos). Este diseño formó la base para conseguir las licencias requeridas, y revisadas, de manera exitosa.
The many benefits of off-site façade manufacture
The high quality of the solution, and of the overall façade, has been enhanced by the fact that the façade has been created off-site as a unitised modular system. Cladding panels, each containing stone, brick, windows and spandrels, have been assembled off-site in factories in Poland and Portugal – then delivered to the site ready to be fixed to the building exterior.
Off-site construction can make a great difference to the detailing and quality of the built product because of the ability to control the conditions in which work is carried out. The panels achieve a high degree of airtightness and weathertightness as well as thermal and acoustic efficiency, with the entire façade designed to slot into place as a unified system.
It also allows for greater programme efficiency because off-site construction can continue when bad weather or other circumstances would otherwise have slowed or suspended construction on site. The recent COVID-19 pandemic required many sites to shut or to slow construction considerably to ensure safe distancing between workers, but off-site construction does not require large site teams working in close proximity. Site safety is also improved by removing the need to carry materials out onto the envelope at the higher levels.
Beneficios de la industrialización de fachadas “off-site”
La alta calidad alcanzada con esa solución de diseño se ha mejorado por el hecho de que la fachada siguió un proceso de industrialización como un sistema modular unificado. Los paneles de revestimiento, cada uno con piedra, ladrillo, ventanas y carpintería, se ensamblaron off-site en fábricas de Polonia y Portugal para luego ser entregados en la obra listos para ser fijados al exterior del edificio.
La industrialización de fachadas marca ya una gran diferencia en la calidad de los detalles y el producto construido debido a la capacidad de controlar las condiciones en las que se realiza el trabajo. Los paneles logran un alto grado de hermeticidad y resistencia a la intemperie, así como eficiencia térmica y acústica, con toda la fachada diseñada para encajar en su lugar concreto como un sistema unificado.
También permite una mayor eficiencia del programa porque la industrialización puede continuar cuando el mal tiempo u otras circunstancias hubieran retrasado o suspendido la construcción en el sitio. La reciente pandemia de COVID-19 requirió que muchos sitios cerraran o desacelerasen considerablemente la construcción para garantizar un distanciamiento seguro entre los trabajadores, pero la industrialización puede controlarse mejor y no requiere equipos grandes en la obra ni cerca de la misma.
Experts in safety-conscious design
It is a fundamental design principle for Chapman Taylor that the health and safety of contractors, residents, maintenance staff, visitors and neighbours is paramount when designing tall buildings, including their façades. Ensuring compliance with current regulations is imperative, as well as considering global best practice to ensure buildings are safe and easily adaptable to meet future requirements and stand the test of time. Our experience in designing and delivering Castle Park View in Bristol is one example among many of our industry-leading knowledge of, and expertise in, how to design tall buildings, whether residential, office or mixed-use, to the highest safety standards while providing attractive, memorable and context-appropriate landmarks on the urban skyline.
Expertos en seguridad o “diseño consciente”
Es un principio de diseño fundamental desde sus inicios, para Chapman Taylor, que la salud y la seguridad de los contratistas, residentes, personal de mantenimiento, visitantes y vecinos es primordial al diseñar edificios altos o de cualquier tipo, incluyendo por supuesto sus fachadas. Es imperativo garantizar el cumplimiento de las regulaciones actuales, así como considerar las mejores prácticas globales para garantizar que los edificios sean seguros y fácilmente adaptables para cumplir con los requisitos futuros y resistir el paso del tiempo.
Nuestra experiencia y trabajo para el diseño y entrega de Castle Park View en Bristol, y en otros muchos proyectos internacionales, incluyendo construcción industrializada, es un ejemplo de nuestro conocimiento internacional y experiencia en diseño como líderes en la industria cuando trabajamos en edificios altos, ya sean residenciales, de oficina o de uso mixto, para ofrecer los más altos estándares de seguridad a la vez que proporcionan un atractivo visual, puntos de referencia memorables y adecuados al contexto en el horizonte urbano.