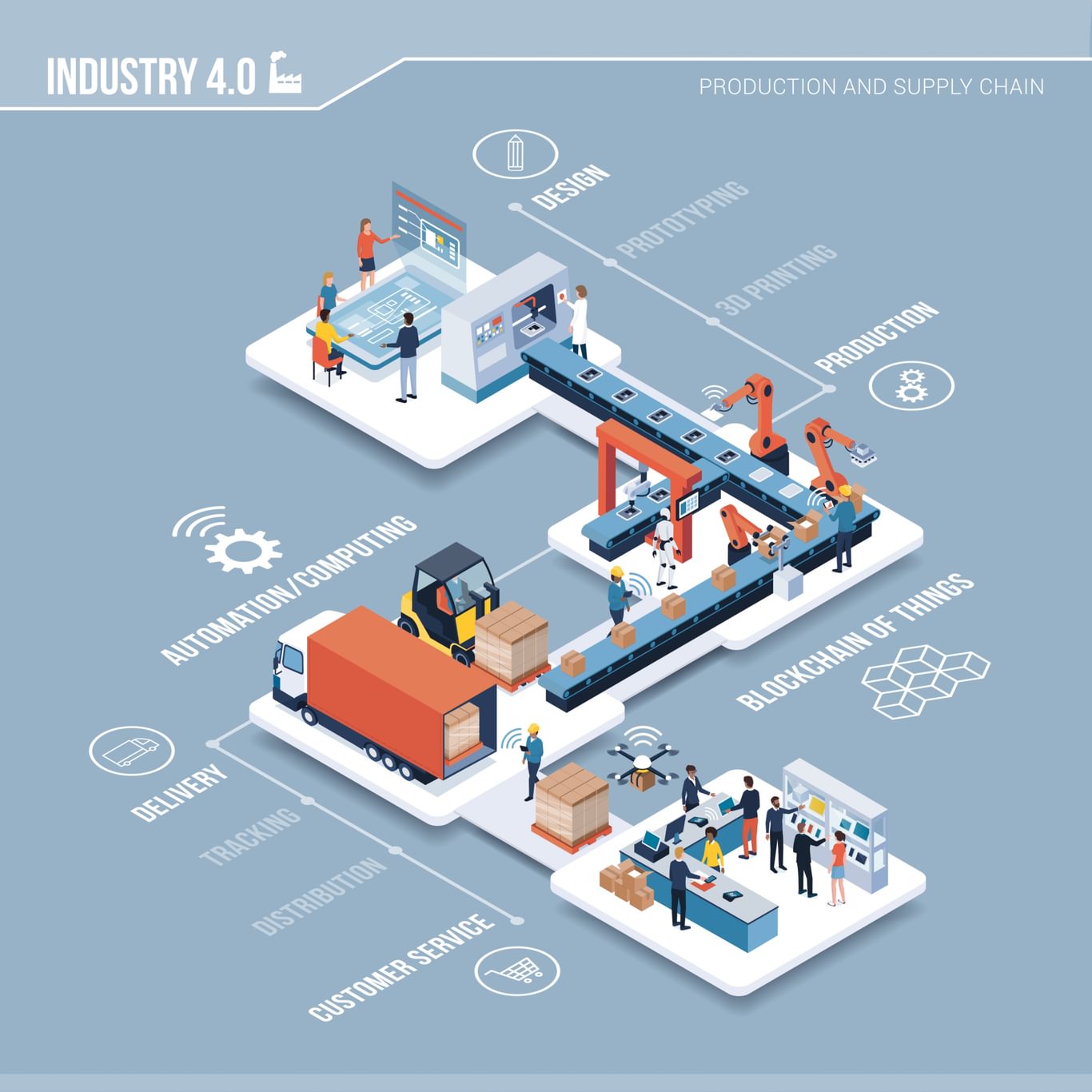
The Factories of the Future
The logistics sector has developed extensive capabilities in predicting and managing demand and purchasing propensities. The next stage in the process, the introduction of “Smart Factories”, will further close the gap between manufacturer, distribution and ultimately customer, says Transportation Director Peter Farmer.
In previous Insight papers, we have explored some of the effects that the drive towards ‘Q Commerce’ is having on the fulfilment sector. We’ve looked at how the sector has responded to the very immediate demand for quicker and greater certainty of delivery. Another trend is emerging that is likely to further revolutionise the process, enabling increased integration between fulfilment and manufacturing.
Factories and Warehouses
The concept of the warehouse has its origin in the stores and granaries of early civilisations, built to house surplus food and produce, largely to help people survive winter or famine. The first known use of the word warehouse dates back to Britain in the 1300s, meaning “a structure or room for the storage of merchandise or commodities.” In other words, a house to store your wares. The growth of national and international trade further stimulated the need for warehousing around marketplaces, ports and in time around rail arteries. The concept of a logistics sector (coming from the French; logistique), first emerged in connection with military logistics.
In relation to early manufacturing, goods tended to be distributed directly from the factory through a dispatch warehouse to the customer. With the pressure for efficiencies, manufacturers looked to reduce stock holding of raw materials as well as finished goods and this allowed the logistics sector to move into this space.
The manufacturing sector continually evolves and adapts to new technologies, from steam to robotics. We are now in the midst of a significant transformation regarding the way we produce products thanks to the digitisation of manufacturing, known as Industry 4.0,[1] coupled with emerging technologies such as 3D printing. The cloud, Internet of Things and information management is making the ‘smart factory’ a reality; an ultra-efficient reality of responding just in time to actual and predicted demand with higher productivity rates and less waste.
People
At Chapman Taylor, we put a lot of emphasis on reinforcing that production and warehousing facilities are workplaces as much as operational facilities. Labour retention is a constant issue for companies, and this is unlikely to change significantly in a 4.0 world.
Over a fifth of the world’s workforce – including 128.9 million people in China and 16.4 million Americans are employed in manufacturing[2]. The sector accounts for roughly 16% of the world’s aggregated economic activity[3], and 27% of China’s GDP. Global crisis aside, the demand for products continues to grow, fuelled by increasing wealth and burgeoning middle-class growth in countries such as China, India and Indonesia.
“The role of humans in the factory of the future will be completely different. Humans will go from planning and performing manufacturing tasks to collaborating with machines, supervising operations, problem-solving, orchestrating innovative solutions and developing technology-based solutions”[4].
A UK government study on ‘The factory of the future’[5] cited the high potential for improved working conditions, equality and gender balance, in the advent of a new focus on creativity, innovation and problem-solving. It went on to reinforce that there will be a continued need for a committed workforce within these facilities.
A shift in emphasis
As we automate as many functions as possible (from founding, forming, manufacturing, fabrication, assembly, maintenance, material supply and finished goods logistics), the factories and warehouses of the future (FoF & WoF) will be increasingly populated by machines and robots with humans patrolling, wrangling, configuring and updating software. Humans will be necessary and a contingency. The spaces will need to be responsive, agile and adaptable. We can already see this in the advanced car manufacturing facilities such as BMW and Tesla and for the warehouse component in leading operators such as Ocado in their Customer Fulfilment Centre (CFC) in Erith in the UK.
We are even seeing this in the construction industry with the increasing popularity of design for manufacture and assembly (DfMA) and ‘off-site construction’. Whole buildings, volumetric elements and building components are being formed in the factory and sometimes even test-assembled in a warehouse prior to shipping to a site.
A key component of the Factory of the Future (FoF) will be research and development, whether in-house or third party. While many of these developments are technology-enabled they are driven by consumer demand. That demand, while having a view toward sustainability, is also driven by innovation and personalisation. Therefore, a fundamental constituent part of the process will be studios and laboratories researching these new features and products.
As well as new methods of production many companies are focusing on new material technology, often resulting in close ties with education and research facilities. These include graphene and nanomaterials, new surface coatings, new composite materials and resins including bio-composites, and biologically derived and natural, living materials.
What does this mean for the design of these buildings?
General
As knowledge of the end customer becomes more closely linked to production, we can envisage closing the gap between, or even colocation of, manufacturing and fulfilment or logistics components. We will be considering buildings with production and distribution combined.
Smaller factories
Some manufacturers are starting to consider that they can produce more in smaller spaces. While larger companies may break down production into small components, with this potential reduction in size some are looking to a more urban location to attract staff
Quality workplace
A quality workplace is important in order to attract and retain staff. Facilities with a ‘wow’ factor, a perception of a light, spacious and clean working environment, quality welfare provision, good workspace utilisation and high visibility with clear lines of sight of all operations. There is a move towards ‘open’, welcoming buildings offering access to customers, suppliers and the general public.
Flexibility
In order to allow innovation and to be responsive to the market, buildings will need to be adaptable and flexible. They will need to be able to be partly or wholly reconfigured, easily and economically. We will need to understand the parameters of these reconfigurations and the demands that they may place on the building. The projects in which Chapman Taylor has been involved with accommodating production lines for end-users have taught us to work with the client to look beyond the initial installation, while still providing an optimum initial business case. One of the key requirements of the Factory of the Future, according to the UK government study is that the facilities need to be ‘agile, reconfigurable factories and extended enterprises.[6]’
Ground Slabs
With increased automation, flatness will be important as will anti-dust finishes. If production lines are likely to be reconfigured from time to time we need to consider the robustness of the slab to be repaired and redrilled for new fixing. We may wish to consider attentive methods of ground slab construction in lieu of monolithic poured slabs. As part of another initiative, Chapman Taylor is investigating hybrid in situ and precast and all precast ground slab solutions, which may provide a more robust as well as sustainable solution.
Thermal performance
If large areas of a facility are not permanently populated by humans and subject to the sensitivity of the produce, process and equipment we may consider reducing the thermal performance of the building fabric and the amount of energy used to condition the production and warehouse environments.
Lighting
If processes and handling are more automated and these areas need to be accessed less by humans, then lighting levels can be reduced. In automated areas, this could be to zero or life safety only, until staff access is required. Humans need good levels of light to carry out tasks and move safely. This is not so with most automated and robot systems. Given that lighting can be as much as 50% of the service loadings in a warehouse environment this could lead to a significant cost, energy and carbon saving.
Power
Increased automation and IT reliance will see increases in power demand. This in turn will increase the demand for sustainable energy sourcing including on-site generation. Some of this may be offset by potential savings in other areas such as lighting above.
Racking
Racking can be closer stacked and potentially higher. However, if the efficiencies in the supply chain are realised then the overall quantum of storage should be proportionally reduced.
External areas
Increased efficiencies and automation may see a reduction in the need for external yard areas as vehicles move more efficiently and distribute more effectively. For larger facilities, moving road trailers around a site by automated tractors to a point where individual drivers may deliver them or take them off, would improve circulation and safety.
Robot wranglers
As production and logistics handling will become increasingly automated the need for human resource will be reduced, apart from the need to monitor and maintain the automation process. A new term “robot wranglers”[7] has been coined to describe this new role. While there is concern about the loss of jobs it should be noted that in many areas of manufacturing there are skill shortages. A recent report by McKinsey Global Institute predicts that new technology will generate between 20-46 million new positions by 2030, while new occupations represent 8-9% of the global workforce. Therefore, staff needs in this manufacturing space will change as companies upskill their workforce to take care of the new automated systems.
As the gap in logistics and manufacturing reduces so will the gap between innovation, personalisation and product development. While manufacturing and distribution may need to be physically co-located, in a 4.0 world development can be remoted and dispersed. We could imagine that many R&D and support functions could even be carried out at home.
What’s next for the sector?
There appears to be no reduction in global demand for things and therefore the industrial sector is likely to continue to grow as it adapts to the fourth revolution. This revolution will radically change the nature of the working environment in production and warehousing facilities and is likely to see the two collocating more.
With the focus on the embodied footprint of our built environment never higher there is also the need to work to close and tighten the circularity of the material cycle. The next significant subject may be how we explore the potential of bringing the product end of life back to the original point of production for reuse or recycling. We have already witnessed IKEA offering to buy back products as part other their ‘Circular Hub’ concept.
“Through buyback, we hope to make circular consumption mainstream; making it easier for customers to acquire, care for and pass on products in circular ways. As we move towards our goal of becoming fully circular and climate positive by 2030 we will continue to take bold steps ensuring that, by then, all products will be made from renewable, recyclable and/or recycled materials; and they will be designed to be re-used, refurbished, re-manufactured or recycled, following circular design principles.”
Peter Jelkeby, retail manager for Ikea UK & Ireland
There is increased interest in the concept with Apple not only offering trade-in but recycling the elements and materials from the trade-in items. Asda has begun selling preloved clothing in 50 of its supermarkets and the likes of Asos, Selfridges and John Lewis selling vintage items.
[1] Industry 4.0 represents the fourth industrial revolution in manufacturing.
[2] https://www.brookings.edu/research/global-manufacturing-scorecard-how-the-us-compares-to-18-other-nations/ [Table 2]
[3] World Bank, 2018, ‘Manufacturing, value add as % of GDP’ (16%)
[4] Dr Lina Huertas, head of technology strategy for digital manufacturing - Manufacturing Technology Centre
[5] https://assets.publishing.serv...
What does this mean for the design of these buildings?
General
As knowledge of the end customer becomes more closely linked to production, we can envisage closing the gap between, or even colocation of, manufacturing and fulfilment or logistics components. We will be considering buildings with production and distribution combined.
Smaller factories
Some manufacturers are starting to consider that they can produce more in smaller spaces. While larger companies may break down production into small components, with this potential reduction in size some are looking to a more urban location to attract staff
Quality workplace
A quality workplace is important in order to attract and retain staff. Facilities with a ‘wow’ factor, a perception of a light, spacious and clean working environment, quality welfare provision, good workspace utilisation and high visibility with clear lines of sight of all operations. There is a move towards ‘open’, welcoming buildings offering access to customers, suppliers and the general public.
Flexibility
In order to allow innovation and to be responsive to the market, buildings will need to be adaptable and flexible. They will need to be able to be partly or wholly reconfigured, easily and economically. We will need to understand the parameters of these reconfigurations and the demands that they may place on the building. The projects in which Chapman Taylor has been involved with accommodating production lines for end-users have taught us to work with the client to look beyond the initial installation, while still providing an optimum initial business case. One of the key requirements of the Factory of the Future, according to the UK government study is that the facilities need to be ‘agile, reconfigurable factories and extended enterprises.’
Ground Slabs
With increased automation, flatness will be important as will anti-dust finishes. If production lines are likely to be reconfigured from time to time we need to consider the robustness of the slab to be repaired and redrilled for new fixing. We may wish to consider attentive methods of ground slab construction in lieu of monolithic poured slabs. As part of another initiative, Chapman Taylor is investigating hybrid in situ and precast and all precast ground slab solutions, which may provide a more robust as well as sustainable solution.
Thermal performance
If large areas of a facility are not permanently populated by humans and subject to the sensitivity of the produce, process and equipment we may consider reducing the thermal performance of the building fabric and the amount of energy used to condition the production and warehouse environments.
Lighting
If processes and handling are more automated and these areas need to be accessed less by humans, then lighting levels can be reduced. In automated areas, this could be to zero or life safety only, until staff access is required. Humans need good levels of light to carry out tasks and move safely. This is not so with most automated and robot systems. Given that lighting can be as much as 50% of the service loadings in a warehouse environment this could lead to a significant cost, energy and carbon saving.
Power
Increased automation and IT reliance will see increases in power demand. This in turn will increase the demand for sustainable energy sourcing including on-site generation. Some of this may be offset by potential savings in other areas such as lighting above.
Racking
Racking can be closer stacked and potentially higher. However, if the efficiencies in the supply chain are realised then the overall quantum of storage should be proportionally reduced.
External areas
Increased efficiencies and automation may see a reduction in the need for external yard areas as vehicles move more efficiently and distribute more effectively. For larger facilities, moving road trailers around a site by automated tractors to a point where individual drivers may deliver them or take them off, would improve circulation and safety.
Robot wranglers
As production and logistics handling will become increasingly automated the need for human resource will be reduced, apart from the need to monitor and maintain the automation process. A new term “robot wranglers” has been coined to describe this new role. While there is concern about the loss of jobs it should be noted that in many areas of manufacturing there are skill shortages. A recent report by McKinsey Global Institute predicts that new technology will generate between 20-46 million new positions by 2030, while new occupations represent 8-9% of the global workforce. Therefore, staff needs in this manufacturing space will change as companies upskill their workforce to take care of the new automated systems.
As the gap in logistics and manufacturing reduces so will the gap between innovation, personalisation and product development. While manufacturing and distribution may need to be physically co-located, in a 4.0 world development can be remoted and dispersed. We could imagine that many R&D and support functions could even be carried out at home.
What’s next for the sector?
There appears to be no reduction in global demand for things and therefore the industrial sector is likely to continue to grow as it adapts to the fourth revolution. This revolution will radically change the nature of the working environment in production and warehousing facilities and is likely to see the two collocating more.
With the focus on the embodied footprint of our built environment never higher there is also the need to work to close and tighten the circularity of the material cycle. The next significant subject may be how we explore the potential of bringing the product end of life back to the original point of production for reuse or recycling. We have already witnessed IKEA offering to buy back products as part other their ‘Circular Hub’ concept.
“Through buyback, we hope to make circular consumption mainstream; making it easier for customers to acquire, care for and pass on products in circular ways. As we move towards our goal of becoming fully circular and climate positive by 2030 we will continue to take bold steps ensuring that, by then, all products will be made from renewable, recyclable and/or recycled materials; and they will be designed to be re-used, refurbished, re-manufactured or recycled, following circular design principles.”
Peter Jelkeby, retail manager for Ikea UK & Ireland
There is increased interest in the concept with Apple not only offering trade-in but recycling the elements and materials from the trade-in items. Asda has begun selling preloved clothing in 50 of its supermarkets and the likes of Asos, Selfridges and John Lewis selling vintage items.
Industry 4.0 represents the fourth industrial revolution in manufacturing.
https://www.brookings.edu/research/global-manufacturing-scorecard-how-the-us-compares-to-18-other-nations/ [Table 2]
World Bank, 2018, ‘Manufacturing, value add as % of GDP’ (16%)
https://assets.publishing.serv...